Table of Contents
I. Introduction to DMAIC Methodology
II. Define Phase in DMAIC Methodology
III. Measure Phase in DMAIC Methodology
IV. Analyze Phase in DMAIC Methodology
V. Improve Phase in DMAIC Methodology
VI. Control Phase in DMAIC Methodology
VII. Benefits of Using DMAIC Methodology
VIII. Comparison with Other Quality Improvement Methodologies
IX. Training and Certification
X. FAQs (Frequently Asked Questions)
I. Introduction to DMAIC Methodology
- What is DMAIC Methodology?
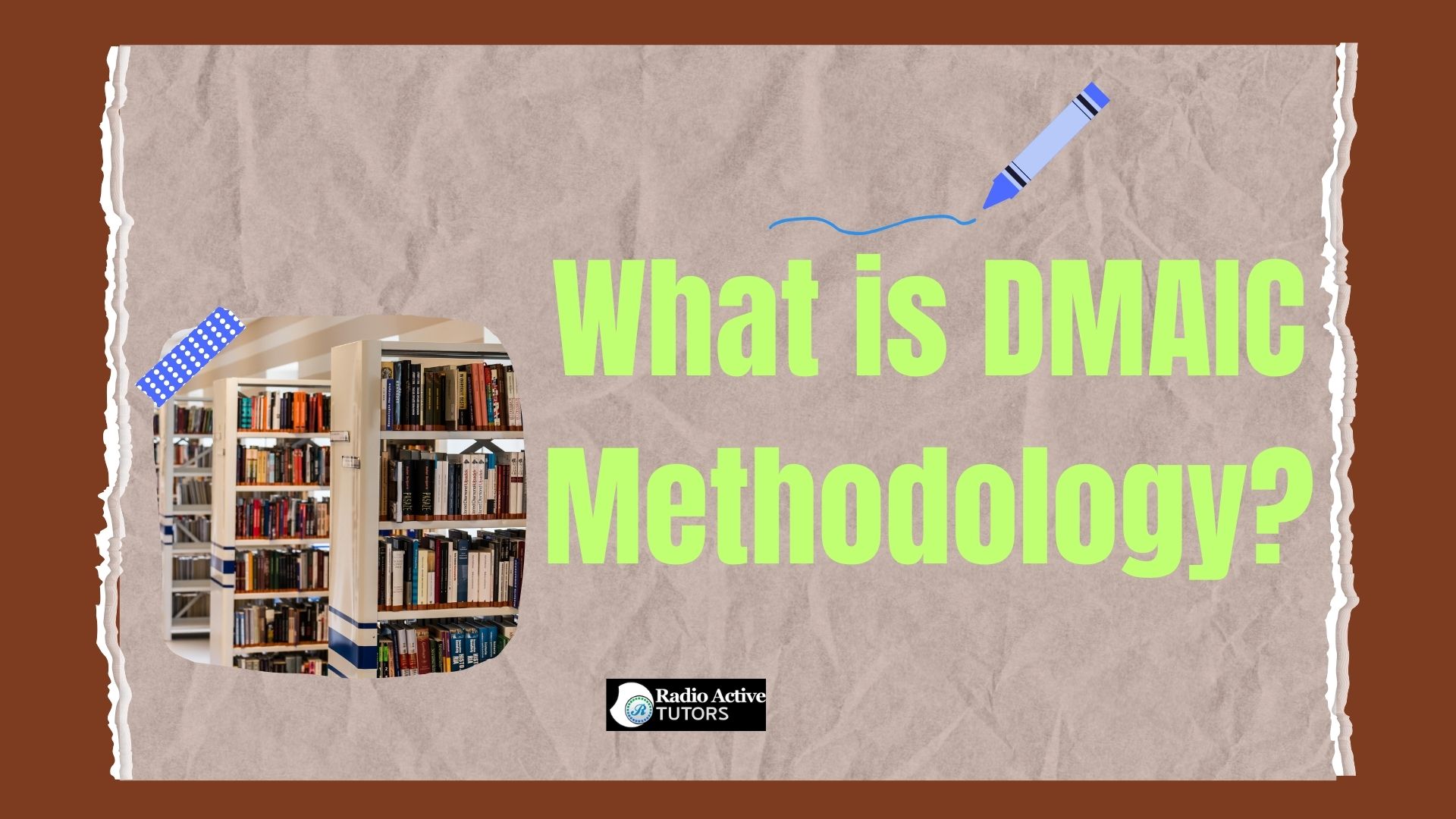
The DMAIC methodology, standing for Define, Measure, Analyze, Improve, and Control, is a structured approach used in process improvement and problem-solving initiatives within organizations. Initially developed as part of Six Sigma practices, DMAIC provides a systematic framework to identify opportunities for improvement, measure existing process performance, analyze root causes of issues, implement effective solutions, and establish controls to sustain improvements over time. Each phase within DMAIC is meticulously designed to ensure that decisions are data-driven, problems are accurately diagnosed, and solutions are both practical and sustainable. By adhering to DMAIC, businesses can achieve significant enhancements in efficiency, quality, and customer satisfaction, thereby fostering a culture of continuous improvement and operational excellence.
- Importance of DMAIC Methodology in process improvement
The DMAIC methodology plays a crucial role in process improvement by providing a structured and systematic approach to addressing issues and enhancing performance within organizations. By following the Define phase, teams can clearly outline project goals and objectives, ensuring alignment with strategic priorities. The Measure phase facilitates the collection and analysis of relevant data, offering a factual basis for understanding current performance levels and identifying areas needing improvement. Analysis in the Analyze phase helps in pinpointing root causes of problems, enabling targeted solutions to be developed in the Improve phase.
Finally, the Control phase ensures that implemented changes are sustained over time through monitoring and establishing controls. This methodical approach not only enhances operational efficiency and quality but also fosters a culture of continuous improvement, ultimately driving long-term success and competitiveness for businesses.
II. Define Phase in DMAIC Methodology
- Objectives and goals of the Define phase
The Define phase in the DMAIC methodology serves as the foundational stage where the objectives and goals of a process improvement project are clearly established. Its primary aim is to define the scope of the project, identify stakeholders, and articulate specific goals that align with organizational strategies and customer requirements. Key activities during this phase include creating a project charter that outlines the project scope, goals, timelines, and resources; conducting initial assessments to understand the current state of the process or problem; and establishing a clear understanding of customer requirements and expectations.
By setting a solid foundation in the Define phase, project teams ensure that subsequent phases of Measure, Analyze, Improve, and Control are focused on addressing the right issues, utilizing appropriate metrics, and ultimately achieving meaningful improvements that contribute to organizational success.
- Key activities and steps involved
The Define phase within the DMAIC methodology encompasses several key activities and steps essential for laying the groundwork of a process improvement project. Firstly, it involves defining the project scope and boundaries to establish clear objectives and deliverables. This is typically documented in a project charter, which outlines the purpose, goals, stakeholders, and constraints of the project. Secondly, teams identify and prioritize customer requirements and expectations through methods such as Voice of Customer (VOC) analysis and stakeholder interviews.
Understanding these inputs ensures that improvements directly address customer needs and enhance satisfaction. Additionally, defining measurable project goals and success criteria helps in quantifying improvements and tracking progress throughout the project lifecycle. Lastly, forming a cross-functional team with diverse expertise and perspectives ensures comprehensive understanding and alignment towards achieving project objectives. By rigorously following these steps, organizations can effectively initiate their DMAIC journey, setting the stage for successful process improvements and sustainable results.
III. Measure Phase in DMAIC Methodology
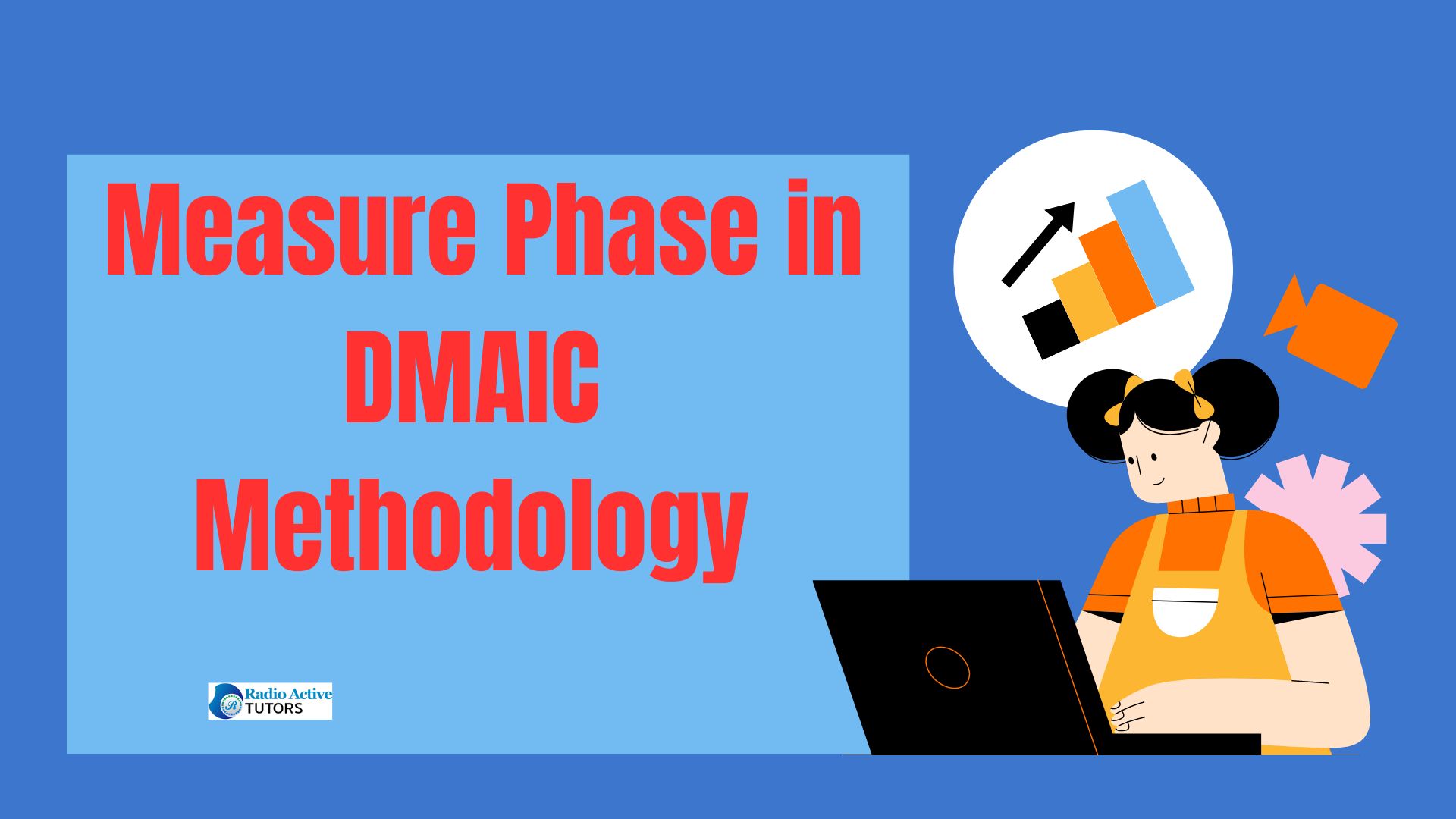
- Purpose and goals of the Measure phase
The Measure phase in the DMAIC methodology serves the critical purpose of establishing a baseline for current process performance and quantifying the extent of the identified problem or opportunity. Its primary goals include collecting accurate data through appropriate measurement techniques to objectively assess the current state of the process, identifying key process metrics that directly impact quality, efficiency, or customer satisfaction, and determining the capability of the process to meet customer requirements.
By meticulously measuring and analyzing data, teams can uncover trends, variations, and potential causes of inefficiencies or defects within the process. This phase sets the stage for informed decision-making in subsequent stages of the DMAIC framework, ensuring that improvement efforts are targeted at addressing root causes and achieving measurable enhancements in process performance.
- Detailed explanation of measurement techniques
In the Measure phase of the DMAIC methodology, selecting and employing the appropriate measurement techniques is crucial for accurately capturing process performance and identifying areas for improvement. Common measurement techniques include data collection methods such as check sheets, surveys, and interviews, which help gather qualitative and quantitative information from various sources. Statistical tools like control charts and histograms are utilized to visualize data, detect patterns, and identify variations in the process.
Additionally, process mapping and flowcharting techniques provide a detailed visual representation of the process flow, helping to pinpoint bottlenecks and inefficiencies. Time studies and work sampling are often used to measure cycle times and understand the time distribution of different process activities. Gauge R&R (Repeatability and Reproducibility) studies ensure that measurement systems are reliable and produce consistent results. By meticulously applying these measurement techniques, teams can establish a comprehensive and accurate baseline of current performance, which is essential for diagnosing problems and guiding data-driven improvements in the subsequent phases of DMAIC.
IV. Analyze Phase in DMAIC Methodology
- Significance of the Analyze phase in DMAIC
The Analyze phase in the DMAIC methodology is significant because it focuses on identifying the root causes of process inefficiencies and defects. This phase builds on the data collected in the Measure phase, using various analytical tools and techniques to uncover the underlying issues that contribute to process problems. Key activities include performing root cause analysis through methods like the 5 Whys, Fishbone (Ishikawa) diagrams, and Pareto charts. Additionally, statistical analysis techniques such as regression analysis and hypothesis testing are used to validate assumptions and identify correlations between variables.
The goal of the Analyze phase is to move beyond surface-level symptoms and understand the fundamental causes of process variation. By doing so, teams can develop targeted and effective solutions in the subsequent Improve phase, ensuring that efforts are focused on addressing the true drivers of poor performance. Ultimately, the Analyze phase is critical for transforming data into actionable insights, leading to more efficient and sustainable process improvements.
- Techniques for root cause analysis
- Fishbone diagram, Pareto analysis, etc.
In the Analyze phase of the DMAIC methodology, several techniques for root cause analysis are employed to identify and understand the underlying causes of process issues. One prominent technique is the Fishbone diagram, also known as the Ishikawa or cause-and-effect diagram. This tool helps teams visually map out all potential factors contributing to a problem, categorizing them into major areas such as People, Methods, Machines, Materials, Measurements, and Environment. Another essential technique is Pareto analysis, which uses the Pareto Principle (80/20 rule) to prioritize problems or causes based on their impact.
By identifying the most significant factors that contribute to the majority of defects or inefficiencies, teams can focus their efforts on the areas that will yield the most substantial improvements. Other techniques include the 5 Whys, which involves repeatedly asking “why” to drill down to the root cause of an issue, and Failure Mode and Effects Analysis (FMEA), which assesses potential failure points and their impact on the process. These techniques collectively enable teams to systematically dissect and understand the problems at hand, paving the way for effective and targeted solutions in the Improve phase.
V. Improve Phase in DMAIC Methodology
- Goals and objectives of the Improve phase
The Improve phase in the DMAIC methodology is focused on developing and implementing solutions that address the root causes identified in the Analyze phase. The primary goals and objectives of this phase are to create effective and sustainable improvements that enhance process performance, efficiency, and quality. Key activities include brainstorming potential solutions, evaluating their feasibility, and selecting the most promising ones. Once solutions are chosen, pilot tests and experiments are conducted to validate their effectiveness and refine them as necessary. The Improve phase also involves optimizing processes to reduce waste, variation, and defects.
By leveraging tools such as Design of Experiments (DOE) and process simulation, teams can predict the impact of changes and ensure they lead to the desired outcomes. Ultimately, the objective is to implement changes that result in measurable improvements, thereby achieving the project’s goals and providing tangible benefits to the organization and its customers.
- Strategies for generating solutions
In the Improve phase of the DMAIC methodology, generating effective solutions is crucial for addressing the root causes of process issues. One common strategy is brainstorming, which encourages team members to propose a wide range of ideas without immediate judgment, fostering creativity and diverse perspectives. Another strategy involves conducting benchmarking studies to identify best practices and innovative solutions used by other organizations or industries. Additionally, utilizing tools such as TRIZ (Theory of Inventive Problem Solving) helps in systematically analyzing problems and generating innovative solutions by applying patterns of invention.
The use of Design of Experiments (DOE) is also critical, as it allows teams to test multiple variables simultaneously to identify optimal conditions and interactions. Prototyping and pilot testing are essential strategies for validating potential solutions in a controlled environment, ensuring their effectiveness before full-scale implementation. Through these strategies, teams can develop robust, data-driven solutions that not only address the identified problems but also enhance overall process performance and efficiency.
- Implementing changes effectively
Implementing changes effectively in the Improve phase of the DMAIC methodology is essential for translating identified solutions into tangible process improvements. This involves careful planning and coordination to ensure that changes are executed smoothly and achieve the desired outcomes. Key steps include developing a detailed implementation plan that outlines tasks, timelines, responsibilities, and resources needed for the change. Engaging and communicating with stakeholders throughout the process is critical to gain buy-in and address any concerns or resistance.
Training and educating team members on new procedures and tools ensure they are well-prepared to adopt the changes. Pilot testing the changes on a small scale helps to identify potential issues and make necessary adjustments before a full rollout. Monitoring and measuring the impact of the changes are essential to ensure they deliver the expected improvements. By following these steps, organizations can effectively implement changes that enhance process efficiency, quality, and overall performance, leading to sustained benefits and continuous improvement.
VI. Control Phase in DMAIC Methodology
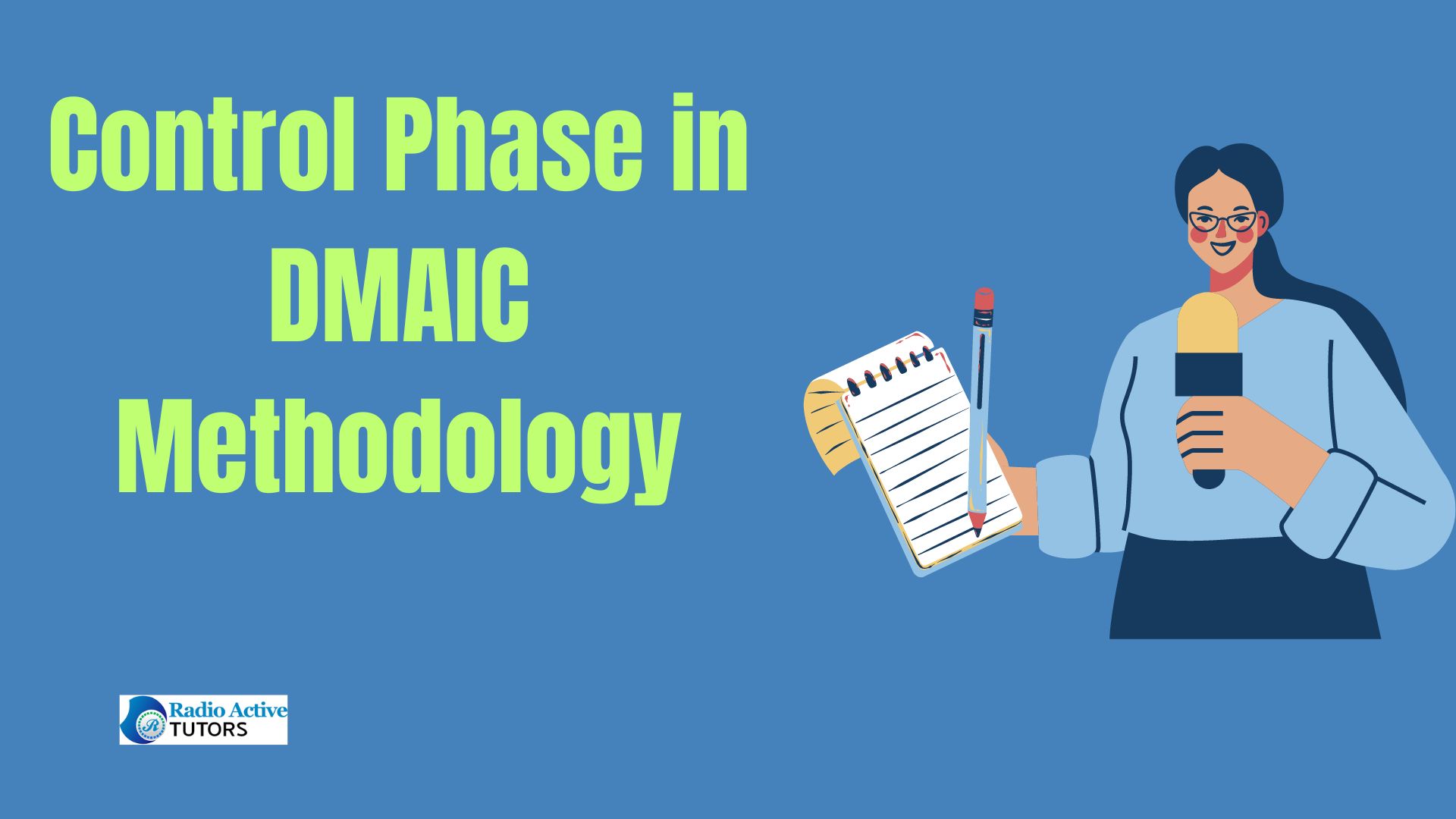
- Importance of the Control phase in sustaining improvements
The Control phase in the DMAIC methodology is crucial for sustaining the improvements achieved in the previous phases. Its primary importance lies in ensuring that the process changes are maintained over time and continue to deliver the desired results. This phase involves establishing standard operating procedures (SOPs), developing monitoring and control plans, and implementing control charts and other tools to track process performance. Regular audits and reviews are conducted to verify adherence to the new standards and to identify any deviations or areas needing further improvement.
Training and ongoing communication with employees help reinforce the importance of the changes and ensure everyone is aligned with the new procedures. By systematically monitoring and controlling the improved process, organizations can prevent regression to old habits, maintain gains in efficiency and quality, and foster a culture of continuous improvement. The Control phase thus ensures that improvements are not only achieved but also sustained, providing lasting value and competitive advantage.
- Tools and techniques for monitoring and control
In the Control phase of the DMAIC methodology, various tools and techniques are utilized to monitor and maintain the improvements achieved in the process. Control charts are one of the primary tools, used to track process performance over time and detect any variations that may indicate potential issues. These charts help in distinguishing between common cause variations, which are inherent to the process, and special cause variations, which signal unexpected changes or problems.
Another essential tool is the development of standard operating procedures (SOPs), which provide detailed guidelines for maintaining the new process standards. Visual management techniques, such as dashboards and scorecards, offer real-time insights into key performance indicators (KPIs) and help in quickly identifying any deviations. Additionally, regular process audits and performance reviews ensure that the improvements are consistently applied and sustained. Employee training and continuous communication also play a vital role in reinforcing the importance of adhering to the new standards. By effectively using these tools and techniques, organizations can ensure that the process remains stable, efficient, and capable of delivering the desired outcomes over the long term.
VII. Benefits of Using DMAIC Methodology
- Quantifiable benefits from DMAIC application
The application of the DMAIC methodology provides numerous quantifiable benefits, significantly enhancing organizational performance and efficiency. By systematically addressing process inefficiencies and defects, DMAIC leads to measurable improvements in key performance indicators such as cycle time, defect rates, and production costs. For instance, organizations often see a reduction in process variability, resulting in higher product quality and customer satisfaction.
Financially, the methodology can drive substantial cost savings by eliminating waste, reducing rework, and optimizing resource utilization. Additionally, DMAIC fosters a data-driven culture, where decisions are based on empirical evidence rather than assumptions, leading to more accurate and effective problem-solving. Productivity gains are also common, as streamlined processes enable faster throughput and better allocation of workforce and materials. Overall, the structured approach of DMAIC not only delivers immediate improvements but also lays the groundwork for sustained operational excellence, providing a significant competitive edge in the market.
- Case studies illustrating successful outcomes
Numerous case studies illustrate the successful outcomes achieved through the application of the DMAIC methodology, highlighting its substantial benefits across various industries. For example, a major automotive manufacturer used DMAIC to address a high defect rate in its assembly line. By meticulously defining the problem, measuring key metrics, analyzing root causes, implementing targeted improvements, and establishing robust controls, the company reduced defects by 60%, resulting in significant cost savings and improved customer satisfaction.
Another case study involves a healthcare provider that applied DMAIC to streamline its patient discharge process. The initiative led to a 30% reduction in discharge time, enhancing patient throughput and satisfaction while reducing operational costs. In the financial sector, a bank utilized DMAIC to enhance its loan processing system, cutting approval times by 50% and boosting customer approval ratings. These case studies underscore how DMAIC’s structured and data-driven approach can drive remarkable improvements in efficiency, quality, and customer experience, delivering tangible and sustained benefits.
- Comparative analysis with other methodologies

When comparing DMAIC with other methodologies, its structured approach and emphasis on data-driven decision-making set it apart as a robust framework for process improvement. Unlike some methodologies that may focus solely on rapid deployment of solutions or qualitative approaches, DMAIC offers a comprehensive and systematic method for problem-solving. For instance, compared to Lean methodology, which emphasizes waste reduction and efficiency, DMAIC includes rigorous measurement and statistical analysis to pinpoint root causes and validate improvements.
Similarly, compared to Agile methodologies, which are often used in software development for iterative improvements, DMAIC’s phased approach ensures thorough problem definition, analysis, and controlled implementation of changes. Six Sigma, another related methodology, shares similarities with DMAIC but focuses more intensely on statistical tools and achieving very high levels of process capability. DMAIC’s versatility lies in its adaptability across industries and its ability to deliver quantifiable results through structured problem-solving, making it a preferred choice for organizations aiming for sustained process excellence and competitive advantage.
VIII. Comparison with Other Quality Improvement Methodologies
- Six Sigma vs. Lean vs. DMAIC
Six Sigma, Lean, and DMAIC are three prominent methodologies in the realm of quality improvement, each offering distinct approaches to achieving operational excellence. Six Sigma focuses on minimizing variation and defects through statistical analysis and aims to achieve a level of quality that meets customer expectations consistently. It employs tools like Statistical Process Control (SPC) and Design of Experiments (DOE) to achieve its goals. Lean methodology, on the other hand, centers on eliminating waste and improving efficiency by streamlining processes and maximizing value for customers.
It utilizes techniques such as Value Stream Mapping and Just-In-Time production to achieve continuous flow and reduce lead times. DMAIC, within the Six Sigma framework, provides a structured problem-solving approach with phases: Define, Measure, Analyze, Improve, and Control. It integrates Lean principles where applicable, focusing on data-driven decision-making and systematic problem-solving to achieve sustainable improvements in processes. While Six Sigma emphasizes statistical rigor, Lean focuses on waste reduction, and DMAIC provides a comprehensive roadmap for problem-solving, organizations often integrate aspects of all three methodologies to tailor approaches that best suit their specific needs and objectives for quality improvement and operational efficiency.
IX. Training and Certification
Training and certification in DMAIC methodology are integral components for individuals and organizations seeking to implement structured process improvements effectively. DMAIC training typically covers the fundamental principles of Define, Measure, Analyze, Improve, and Control phases within the Six Sigma framework. Participants learn various statistical tools and techniques essential for data-driven decision-making and problem-solving. Certification programs offer formal recognition of proficiency in DMAIC, validating individuals’ capability to lead or contribute to improvement projects with measurable outcomes.
These programs are often structured with different levels of certification (e.g., Yellow Belt, Green Belt, Black Belt) corresponding to varying levels of expertise and responsibilities. Certification not only enhances individual skill sets but also demonstrates organizational commitment to quality and continuous improvement. By equipping professionals with DMAIC training and certification, businesses can foster a culture of excellence, drive operational efficiencies, and achieve sustainable business results.
X. FAQs (Frequently Asked Questions)
- What are the primary steps of DMAIC Methodology?
- How long does a typical DMAIC Methodology project last?
- What industries benefit the most from DMAIC Methodology?
- Is DMAIC Methodology suitable for small businesses?
- What industries benefit most from DMAIC Methodology?
- How long does a typical DMAIC Methodology project take?
- What are the main challenges in DMAIC implementation?
- Can DMAIC Methodology be combined with Agile methodologies?
- What role does leadership play in successful DMAIC projects?
- How can small businesses benefit from DMAIC Methodology?
- Is DMAIC Methodology suitable for continuous improvement initiatives?
- What are some real-world examples of DMAIC Methodology success stories?
- How does DMAIC Methodology contribute to organizational culture?
- What are the prerequisites for learning DMAIC Methodology?